Toplogy Study
SOLIDWORKS Simulation study of a cantilever beam to optimise stiffness to weight ratio
Powerful tool to make lighter parts for use in areospace or automotive industries where difficult to manufacture, shape optimisied, light weight parts are required
The initial forces and fixtures are defined on a part. A plane of symmetry is also defined to reduce computation time. Manufacturing constraints have also been defined around each bolt hole for threadding tolerance
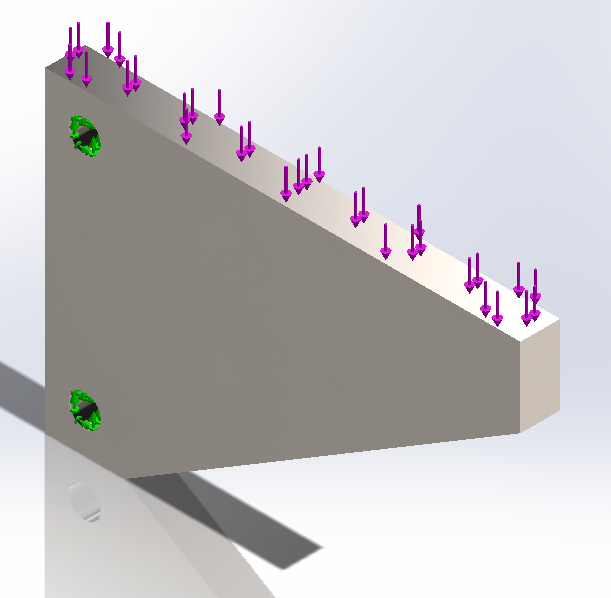
Smooth mesh produced from simulation results. Below image is 40% mass where deflection is below required limit
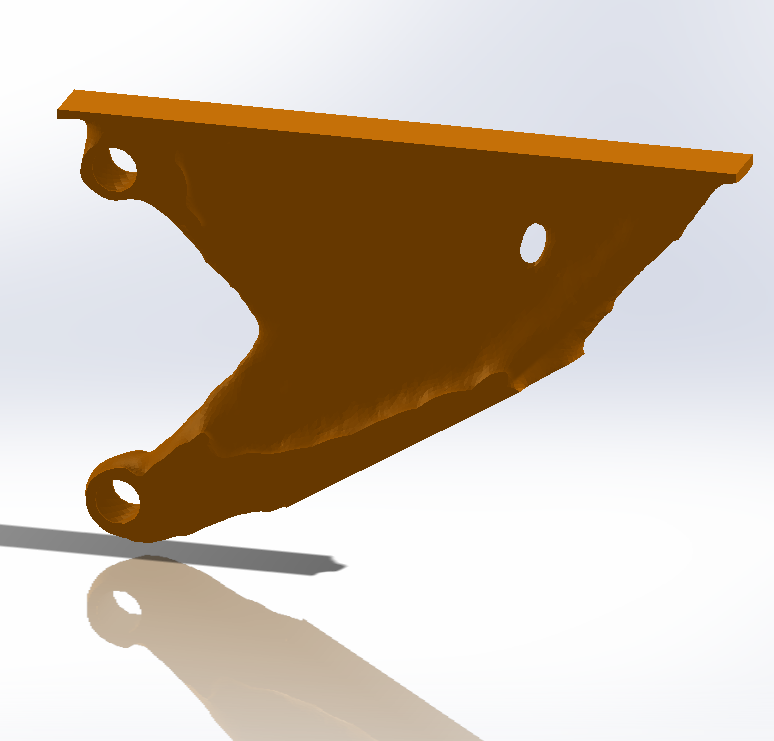
Image below shows part of which its design is inspired by the topology optimisation shown above
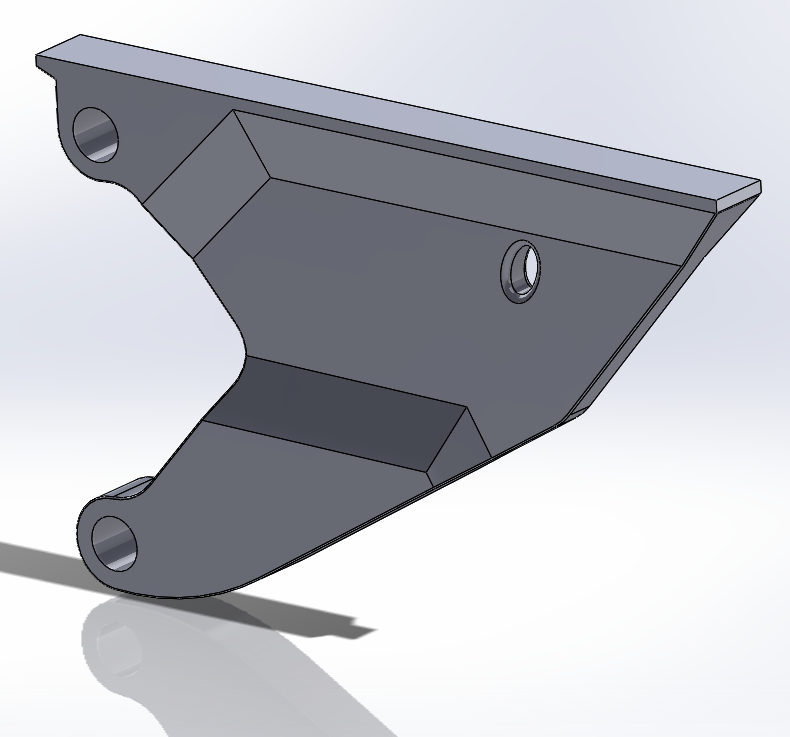
Below shows simulation study of first iteration of the toplogy optimised part. The deflection is over the required limit and so the design must be changed.
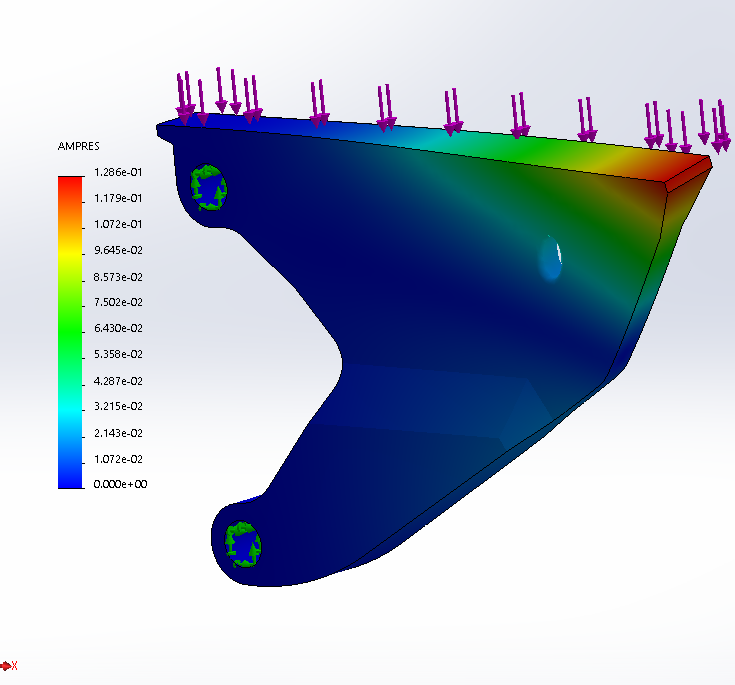
Below shows the second iteration of the designed part inspired by the topology optimised part
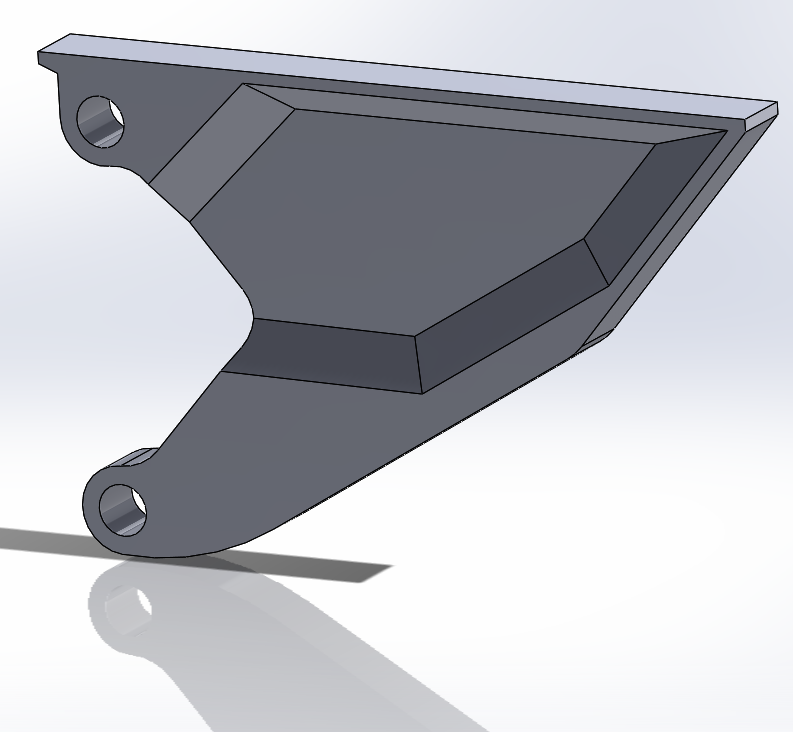
The simulation results shown below is under the required limit of deflection and so this is the final design of the cantilever
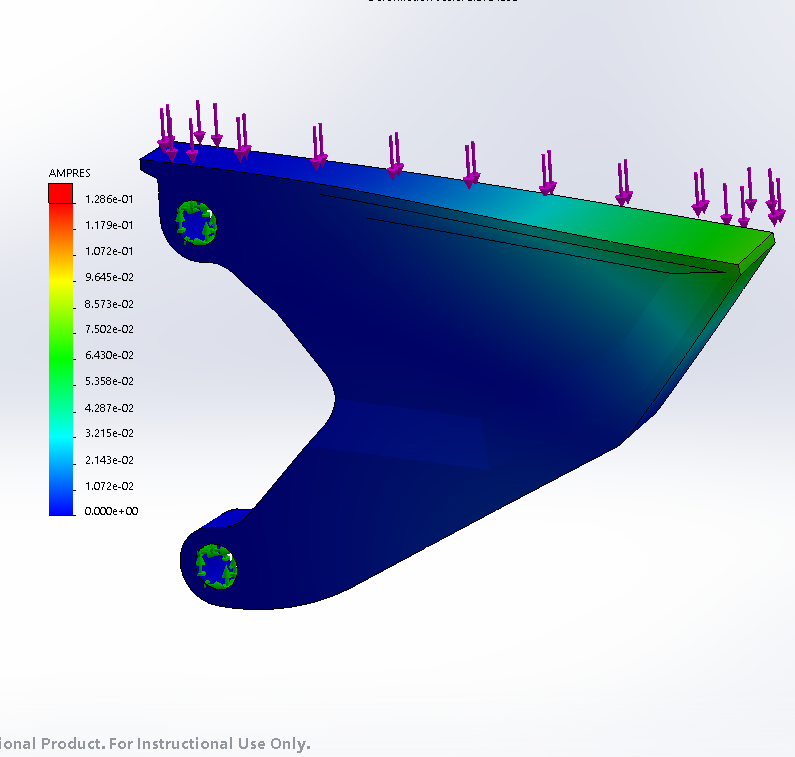
Further iterations could be done to further decrease mass of the part however, this will not be necessary as this is just an example study
This is a powerful tool that greatly accelerates the design process for parts requiring high stiffness to mass ratio